Issues in plastic routing
With the multiplicity of plastic materials in today’s industry, issues in machining can and will happen. Plastics vary significantly through-out the manufacturing process, and these inconsistencies combined with a never ending list of applications can lead to an abundance of issues. This article will address common issues with plastic routing.

Issue #1: The chips become welded to the cutting tool and/or product being cut Issue
One of the most frustrating problems CNC operators comes across when cutting plastics is welding of chips to the cutting tool or the part being cut. The chip(s) is a result of heat transfer from the tool to the part being routed. This transfer of heat can cause the chip to weld to the router tool or the part being cut. This occurrence can prove to be costly to a manufacturer in terms of scrap rate and time. This however, can be avoided. In addition to poor tool selection, chips can occur because of unsuitable chipload. Chipload is defined by, the thickness of the chip. The chip is formed as a result of spindle speed, feedrate, and the quantity of edges the router tool will cut in a cycle. Chipload can also influence the finish, as we will discuss later.
The fact is that plastics are generally quite sensitive to heat, especially under max speeds and feed rates. The trick is to produce a reasonable sized chip. However, simply increasing the feedrate to increase chip size is not enough. For example, feedrate is limited in the production of smaller parts. To remedy this, your spindle speed must be employed to maximize chipload.
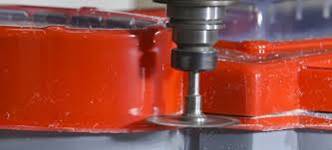
The chipload formula is as follows:
Chipload = Feedrate
RPM x # of cutting edges
Other factors that may be contributing to chip welding:
- The use of small diameter tools. There is limited chip clearance when using a small diameter tool. As a result, the chips have no clearance, and simply get recut. It’s the re-cutting of the chips that cause welding.
- If the chip is being influenced insufficiently, the geometry of the router will be compromised. Taking time to ensure that you’re making the proper angular cuts in the proper spaces should maximise chipload thus reducing chip weld.
- The direction in which you’re cutting can also contribute to the above issue. To remedy this, we recommend that you use conventional cutting direction.
Issue #2: The product has a poor finish
If your company uses signs, P-O-P displays or exhibits to promote your product(s) then the finish is extremely important, as the public can view and scrutinize any inconsistencies. Needless to say, this can have undesirable effects on the image of your company. In order to maximise a quality finish, you must choose the proper tool. Once again, proper chipload rates can give you the desired effects you’re looking for and the range for an exceptional finish is known to occur between 0.004 and 0.012.
Further, a sufficient sized chip will remove cratered finishes on hard plastic projects and unnecessary knife marks in soft plastic projects.
In addition to chipload, the general condition of the CNC machine, as well as, improperly holding parts can contribute to a poor finish. For example, CNC routers integrate the use of spoilboard systems. The spoilerboard allows a vacuum to hold down the part being cut. A poorly designed spoilboard system will reduce maximum suction. The part being cut may move out of place as a result of poor suction which can ultimately cause a poor finish.
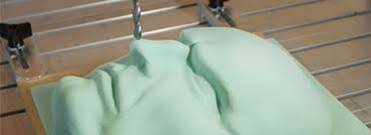
Whether you want to reduce chip weld, or maximise an outstanding finish, the key is in understanding the material being cut. Further, proper chipload rate to spindle speed will allow you to find a sweet spot that will allow for minimal chip weld, as well as, a good finish. Also, ensure you choose router tools with geometry specific to plastic. As well, maintaining your CNC router and using a dependable spoilerboard should not only increase production but also decrease scrap rate and produce a finish that is worthy of your product.
CanCam CNC Routers Can Cut:
Plastic:
ABS, Polycarbonate, Polyethylene, PVC, Polypropylene, Polystyrene, Cast and Extruded Acrylic, HDPE, UHMW, Marine PVC, Lexan, Phenolic, Sintra, Nylon, Lucite, Solid Surface Materials, Luan, PET, Acetate, VHMW, Mica.