Tips for tackling aluminum with CNC routers.
CanCam has a large variety of CNC Routers for aluminum, bronze and copper. At one point or another, you’re going to push the limits of what your machine is capable of doing. Listed below, are a number of suggestions that can aid you in your aluminum cutting endeavors. Good luck!
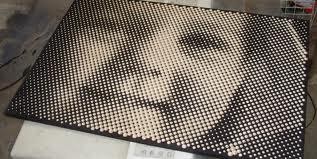
- Using the right tools for the job
A CNC Router can be an ideal tool for cutting aluminum. Using the wrong tool for the job can decrease your chances of success and prove to be quite costly in the end. Using a solid carbide single flute bit is a common tool.
- Using a Feeds and Speeds Calculator
Once you have the right tools to do the job, you’ll want to locate a Feeds and Speeds calculator. In the past, machinists would “cut by ear”. However, times have changed resulting in much faster feeds and speeds rates. A Feeds and Speeds Calculator replaces the “ear” and even the most novice of CNC’ers can benefit. The manufacture of the tool bit will also typicaly advise on max spindle speeds and feeds to be used with that specific tool.
After referring to your feeds and speeds calculator, your first problem will be dealing with the recommended rpms being too low. One of the issues for most CNC routers is the spindle goes fast compared to most CNC mills. Your average CNC mill will max out at 6,000 rpm and many CNC routers can’t go that slow. Life for the CNC router begins around 10,000 rpm.
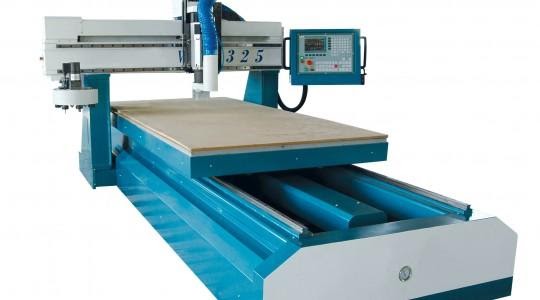
- Always clear away chips
One of the biggest problems that contribute to broken bits and chip welds is the re-cutting of chips. To avoid this, ensure you always clear chips away from the cutting face. Further, you can’t always rely on your vacuum system to collect every last bit of debris. A more dependable solution would be, fixing an air blast directly to the spindle. This air blast can be pointed directly above where the cutting tool meets the material being cut. A great example of this type is CanCam’s PRO1325. The PRO 1325 also offers a stationary gantry for extra stability along with a heavy duty stress relieved frame weighing in at 3000Kg. A pneumatic counterbalance system supports the Z axis. A centralized automatic lubrication system services all positioning bearings, ball screws and racks.
- Use a Mist to Lubricate
After clearing away all debris, your next problem is providing adequate lubrication to the cut. Adequate lube will deter chips from sticking to cut edges. Either way, lubricant should be used with all aluminum projects. Assuming you have an air blast rigged to your unit, it is appropriate to course a coolant mist through the same device. In addition to Cancam’s PRO1325, we also offer a Microdrop Misting Unit. The Microdrop Misting Unit is capable of producing as little as 1 mL/min creating an adequate mist that will make your task much easier.
- Carbide coated cutters are highly recommended
One method you can employ to increase the recommended rpm is to ensure you’re using cutters that are capable of going that fast and a TiAlN coating will give the cutter the ability to cut even faster. The TiAlN coated cutter costs a little more, but the difference pays for itself.
- Derate for rigidity by limiting your horsepower
The cutting force needed to cut metals is usually higher than the cutting force needed to cut wood and CNC Routers are significantly less rigid than CNC Mills. It’s difficult to know the exact rigidity of a given machine, so we can use spindle power as an alternative. Using a feeds and speeds calculator will give you the calculations needed to de-rate spindle power that matches the project specs and overall weight of your machine to a spindle command that is suitable for that level of rigidity.
- Don’t slow down the feedrate too much!
Going too slow on your federate may cause your tool to rub rather than cut. You’ll want to keep the cutter moving smoothly if you want to maintain the recommended chiploads with the rpms cutting that high.
Moreover, CanCam has routers for cutting aluminum and brass,iIt’s just a matter of matching your machine’s abilities to the feeds and speeds requisite of the material. This can easily be done by sufficient cutting parameters and wise tool selection. Add to that the use of lubrication and a habit of keeping the cut free of chips and you should be ready to take on an aluminum project.
Metals CanCam CNC Routers Can Cut:
Aluminum, Brass, Copper, Bronze
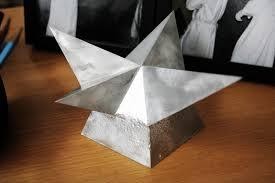